Introduction
The impact crusher is widely recognized for its high crushing efficiency and low energy consumption, making it a staple in industries such as mining, construction, and chemicals. However, the wear and tear of its components pose a significant challenge, reducing equipment lifespan and operational efficiency. This article examines the selection of wear-resistant materials and strategies to improve the performance of impact crusher parts.
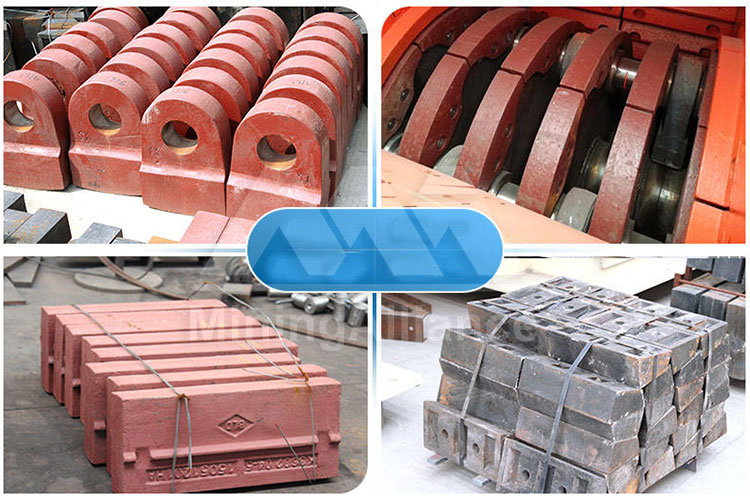
Selection of Wear-Resistant Materials
1. High-Chromium Cast Iron
High-chromium cast iron stands out due to its remarkable hardness and wear resistance, making it an excellent choice for blow bars and impact plates. For example, cast iron with 20% chromium content can achieve a hardness exceeding HRC60, greatly extending part lifespan, especially when processing hard materials.
2. Composite Materials
Ceramic-metal composites have emerged as a promising option in recent years. For instance, ceramic-reinforced high-manganese steel blow bars integrate the toughness of high-manganese steel with the superior wear resistance of ceramics, performing exceptionally well under high-impact and severe wear conditions.
3. Alloy Steel
Low-alloy steel, valued for its toughness and strength, is frequently used in impact plate supports and frames. Adjusting alloy composition and applying heat treatment can further enhance its overall performance.
Strategies for Performance Enhancement
1. Optimized Heat Treatment
Quenching followed by low-temperature tempering enhances both hardness and toughness. For example, blow bars tempered at 200°C after quenching retain high hardness while minimizing brittleness risks.
2. Surface Treatment Technologies
Techniques like laser cladding or thermal spraying apply wear-resistant coatings to part surfaces. Applying a tungsten carbide layer to an impact plate, for instance, significantly boosts its resistance to impact and wear.
3. Structural Design Improvements
Finite Element Analysis (FEA) optimizes part shapes to reduce stress concentrations. Adjusting blow bar geometry, for example, ensures even stress distribution during operation, prolonging service life.
Practical Application Cases
1. Mining Operations
In a granite mine, high-chromium cast iron blow bars increased part lifespan by 35% and crushing efficiency by 10%.
2. Construction Waste Recycling
In a construction waste processing project, composite material impact plates extended maintenance intervals by 40%, reducing operational costs substantially.
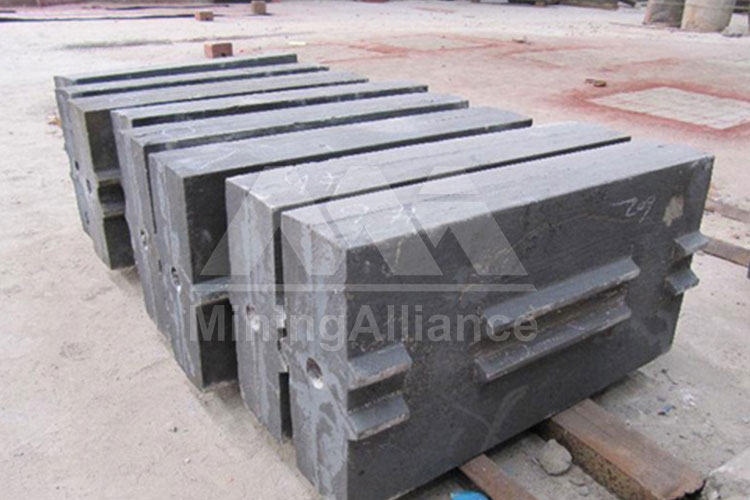
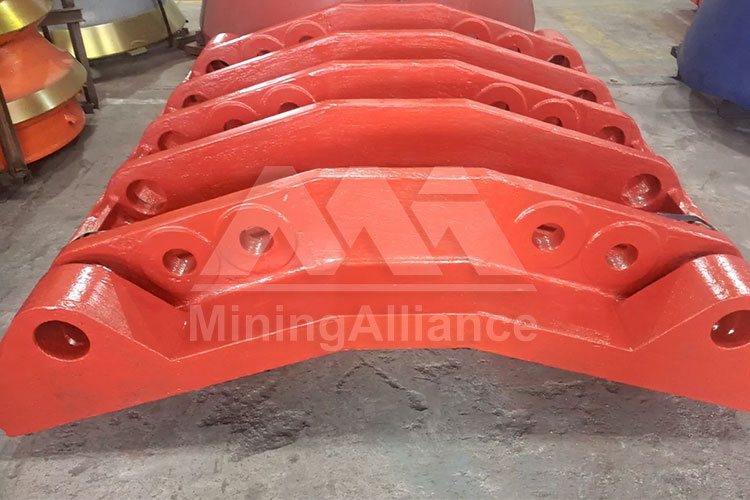
Future Development Directions
Advancements in material science promise the adoption of nano-composite materials and self-healing materials for impact crusher parts. These innovations, leveraging microstructural optimization or self-repair capabilities, will further improve wear resistance and durability.
Choosing appropriate wear-resistant materials and implementing performance-enhancing strategies are vital for extending the lifespan of impact crusher parts and boosting equipment efficiency. With proper material selection and process optimization, parts can excel even in the harshest environments.