Introduction
The manufacturing processes and quality assurance of impact crusher parts directly influence their performance under high-stress conditions. High-quality production workflows and stringent quality controls are essential to ensure equipment reliability. This article explores the manufacturing processes and critical quality assurance measures for these components.
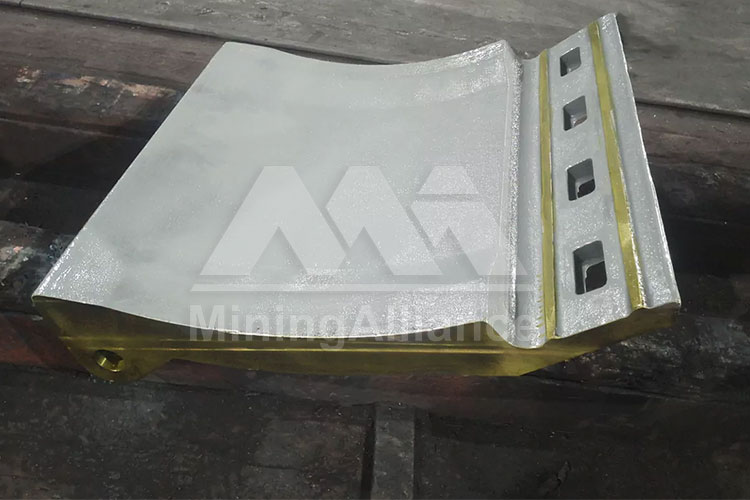
Manufacturing Process Workflow
1. Casting Technology
Blow bars and impact plates are typically produced via lost foam casting or sand casting. Lost foam casting minimizes internal defects like porosity and inclusions, yielding blow bars with high surface smoothness and dimensional accuracy within ±1.5mm.
2. Precision Machining
Machining involves turning, milling, and drilling. For example, eccentric shafts undergo CNC machining to ensure coaxiality and surface roughness align with design specifications, improving assembly precision.
3. Heat Treatment Processes
Heat treatment is pivotal for enhancing part performance. Post-casting, blow bars are quenched and tempered to achieve a hardness of HRC55-58 while maintaining sufficient toughness to withstand impact loads.
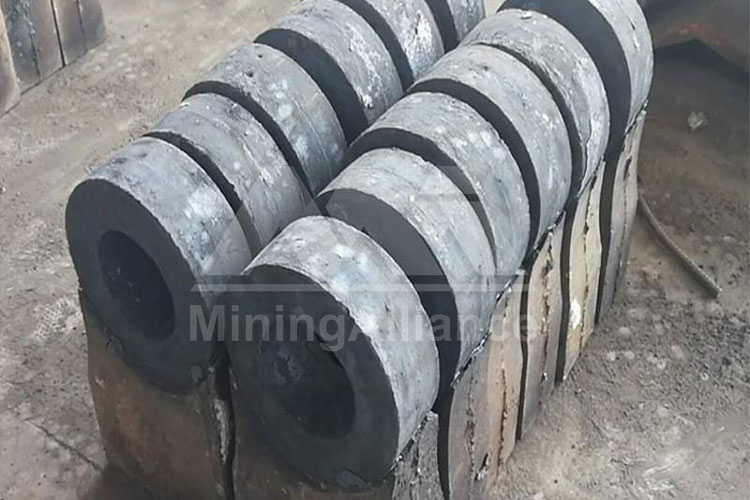
Quality Assurance Measures
1. Raw Material Inspection
Chemical composition analysis and metallographic inspection verify raw material quality. For instance, high-chromium cast iron requires chromium content between 18% and 25% to guarantee wear resistance.
2. Process Monitoring
Ultrasonic testing and X-ray inspection during casting and machining detect internal cracks or porosity. Blow bar castings, for example, must pass ultrasonic testing to confirm the absence of significant defects.
3. Finished Product Testing
Finished parts undergo comprehensive testing for hardness, toughness, and dimensional accuracy. Impact plates, for instance, must exhibit a hardness above HRC50 and an impact toughness of at least 12J/cm².
Application Case Analysis
1. Aggregate Production
In an aggregate plant, optimized casting and heat treatment processes extended blow bar lifespan by 20%, reducing maintenance downtime.
2. Cement Industry
In cement clinker crushing equipment, high-precision machined impact plate supports enhanced operational stability and increased crushing efficiency by 15%.
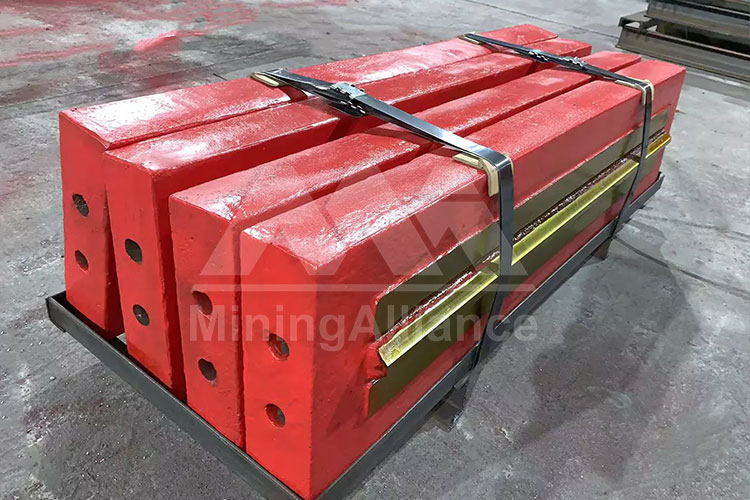
Future Trends
Smart manufacturing technologies, such as digital casting and real-time quality monitoring systems, will elevate the precision and consistency of part production. Looking ahead, 3D printing may enable small-batch production of complex parts.
Advanced manufacturing processes and a robust quality assurance framework are the foundation of high-performance impact crusher parts. Through process innovation and optimized quality management, these components can deliver reliable performance across diverse operating conditions.